CONCRETE
reliquary wall
My involvement with the Cathedral initially started with the simple exercise of establishing a joint pattern for the Reliquary Wall formwork that would be re-used across six different pours. Given that the walls were both curved and sloped, we had to quickly devise a system to simply and accurately translate the expression of curvilinear 3D form into 2D drawings. We also had to provide a means to establish the geometry of the formwork for windows, doors, and other openings carved out of the form. We found that the most effective method to communicate was to share and exchange 3D subtraction models which were translated into shop drawings. Not only did we use the files amongst the design team, we were able to use the same models to communicate and work with the concrete subcontractor.
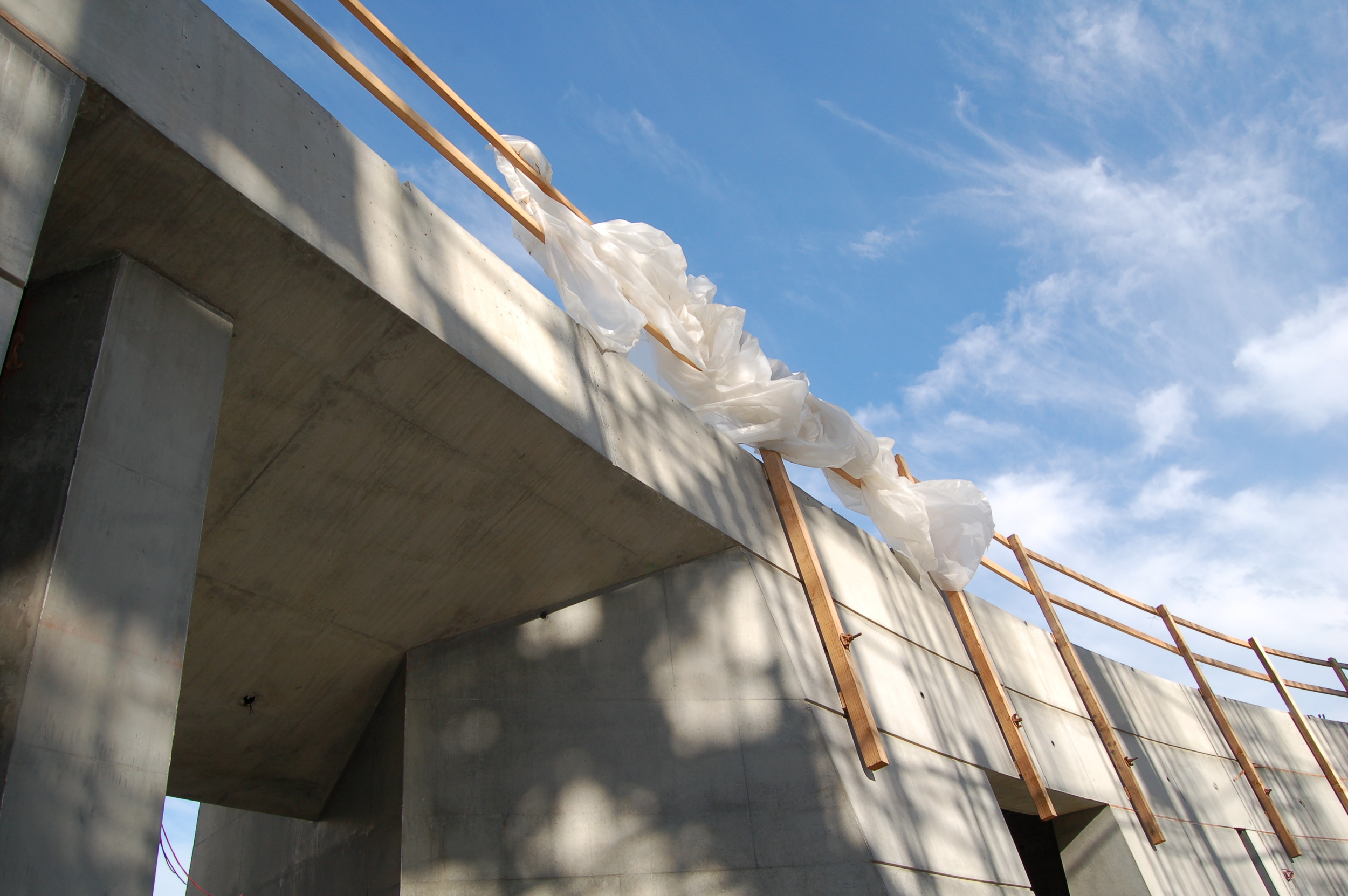
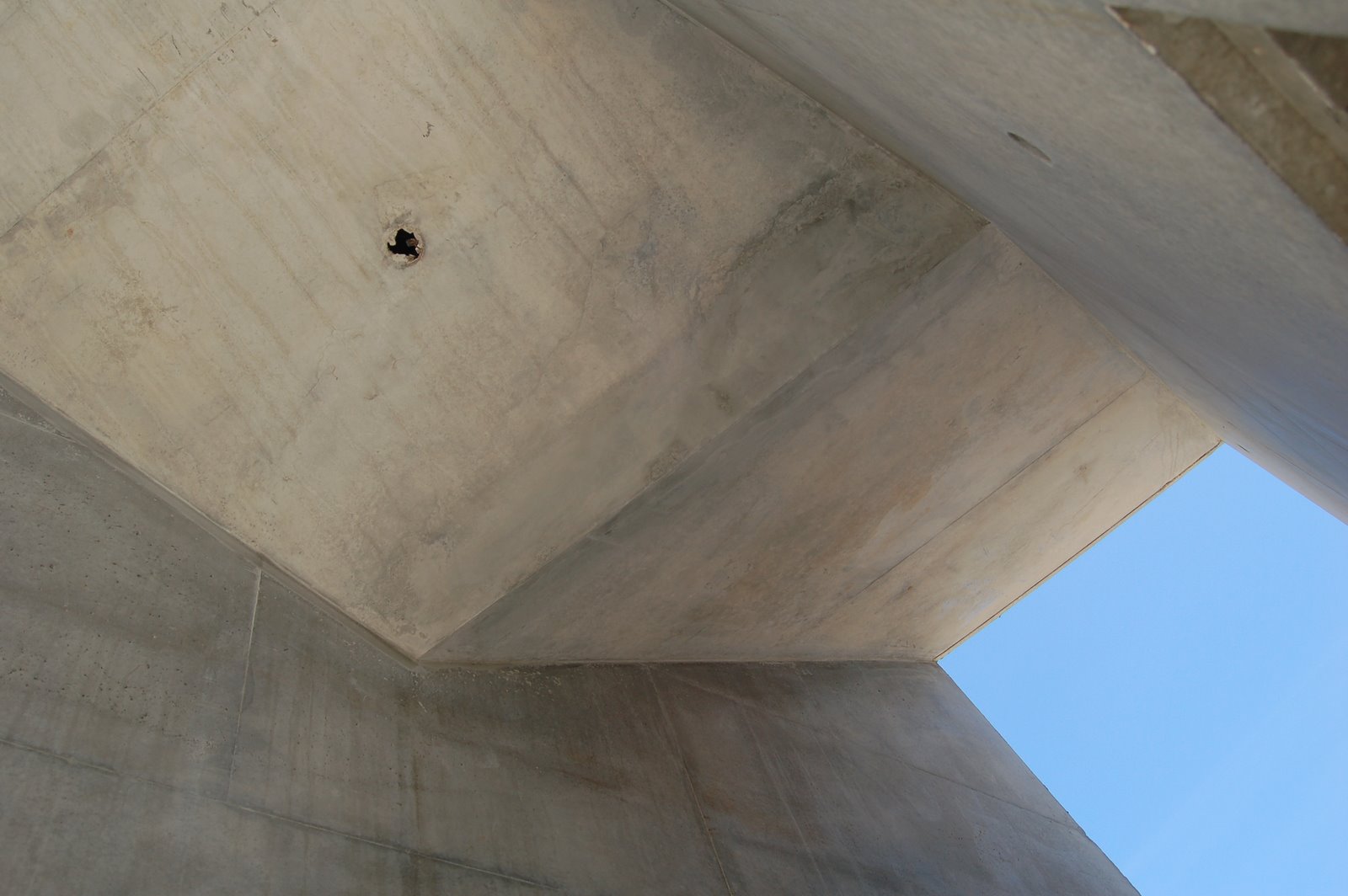
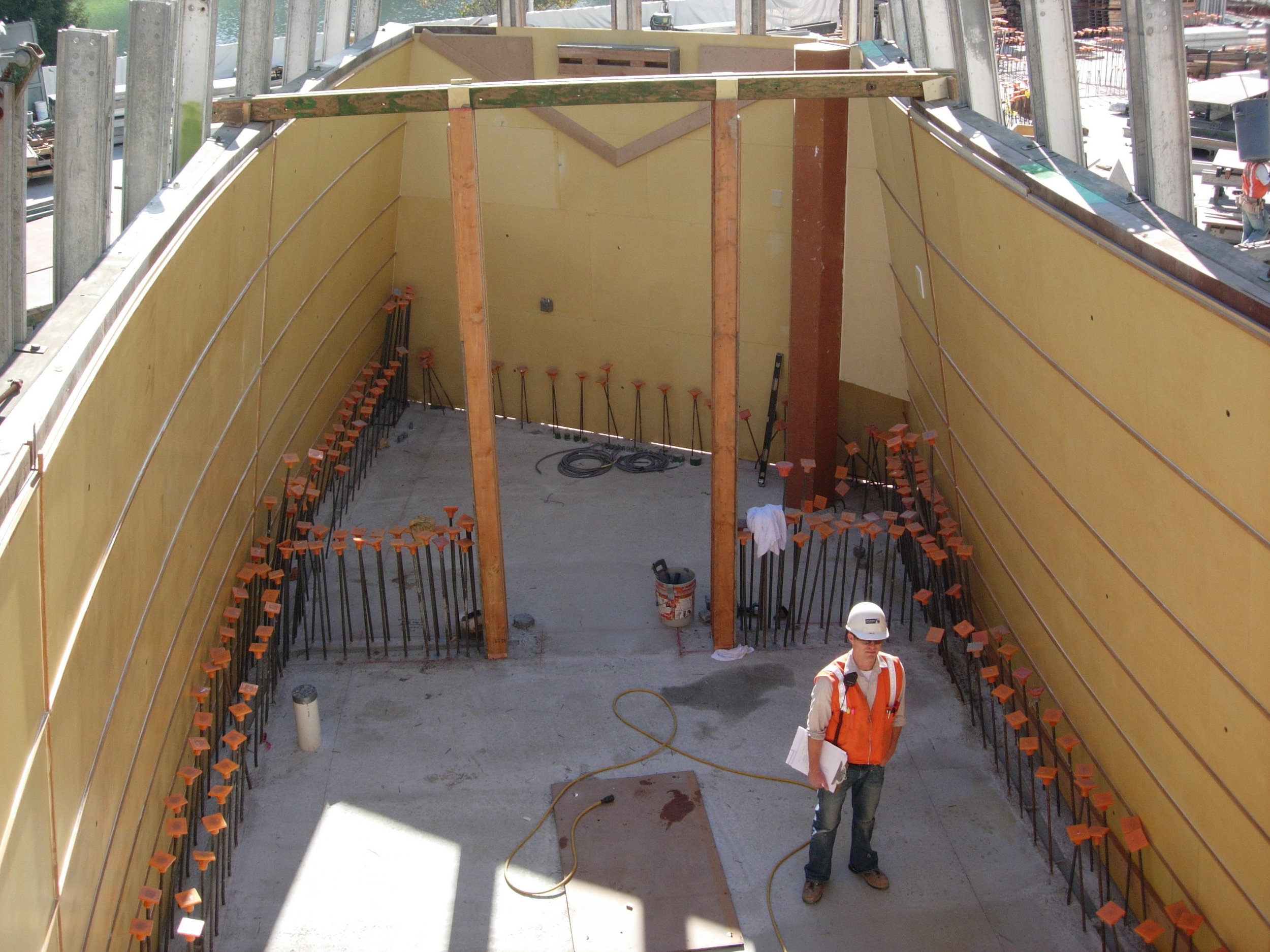
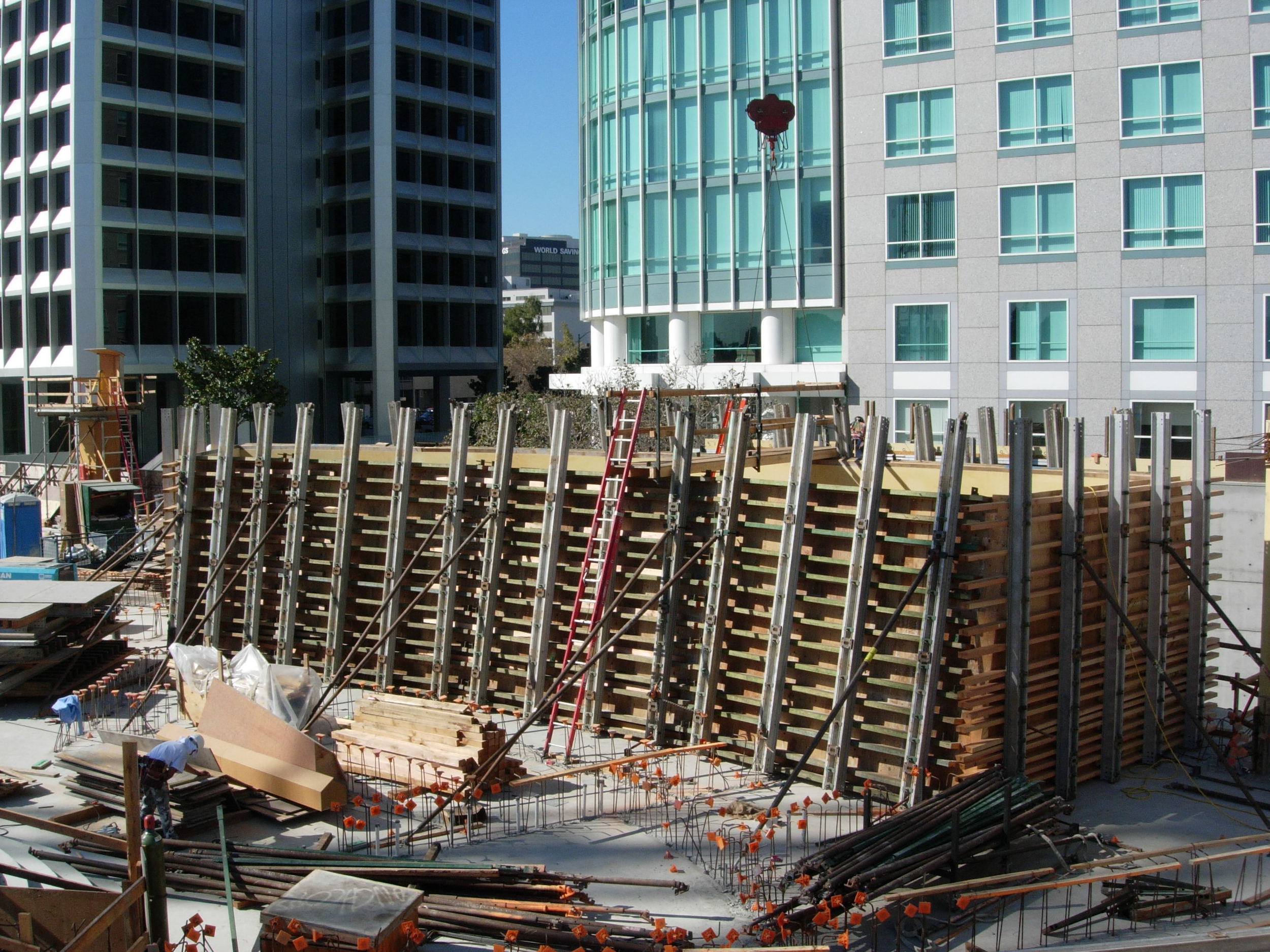
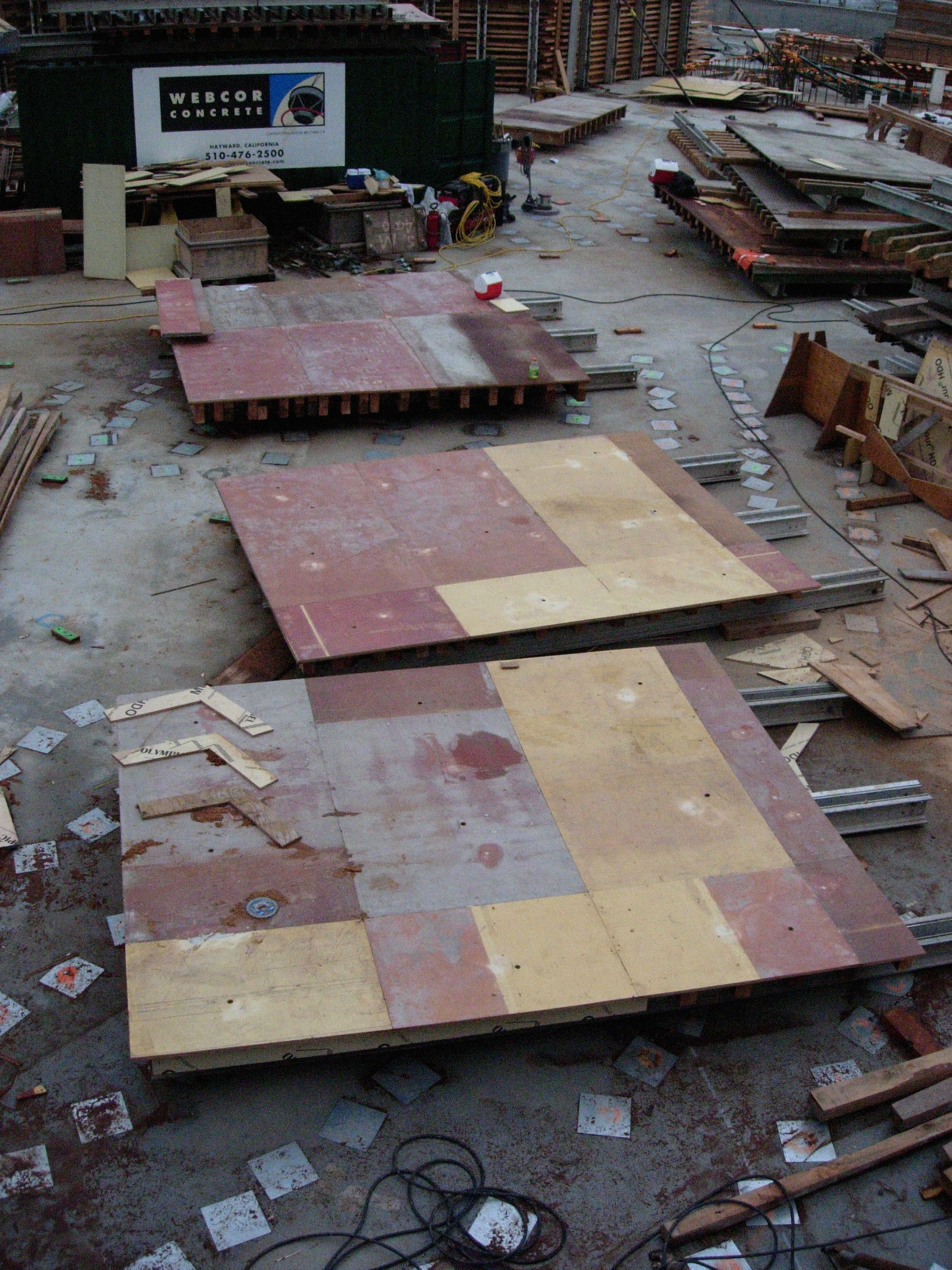
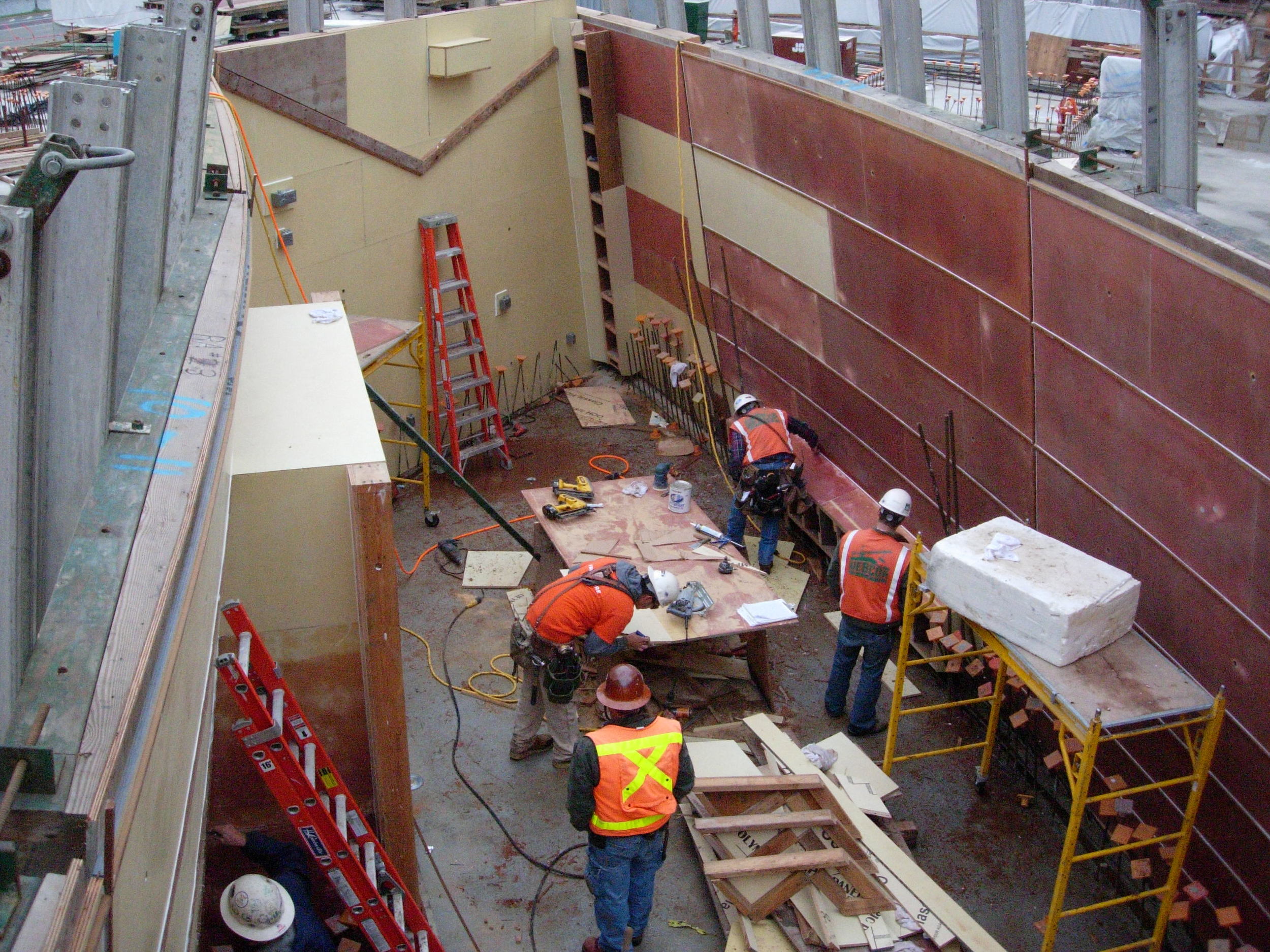
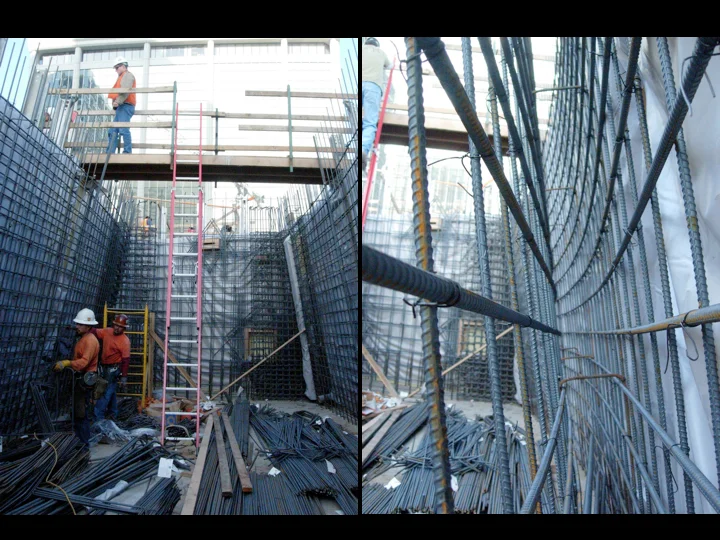

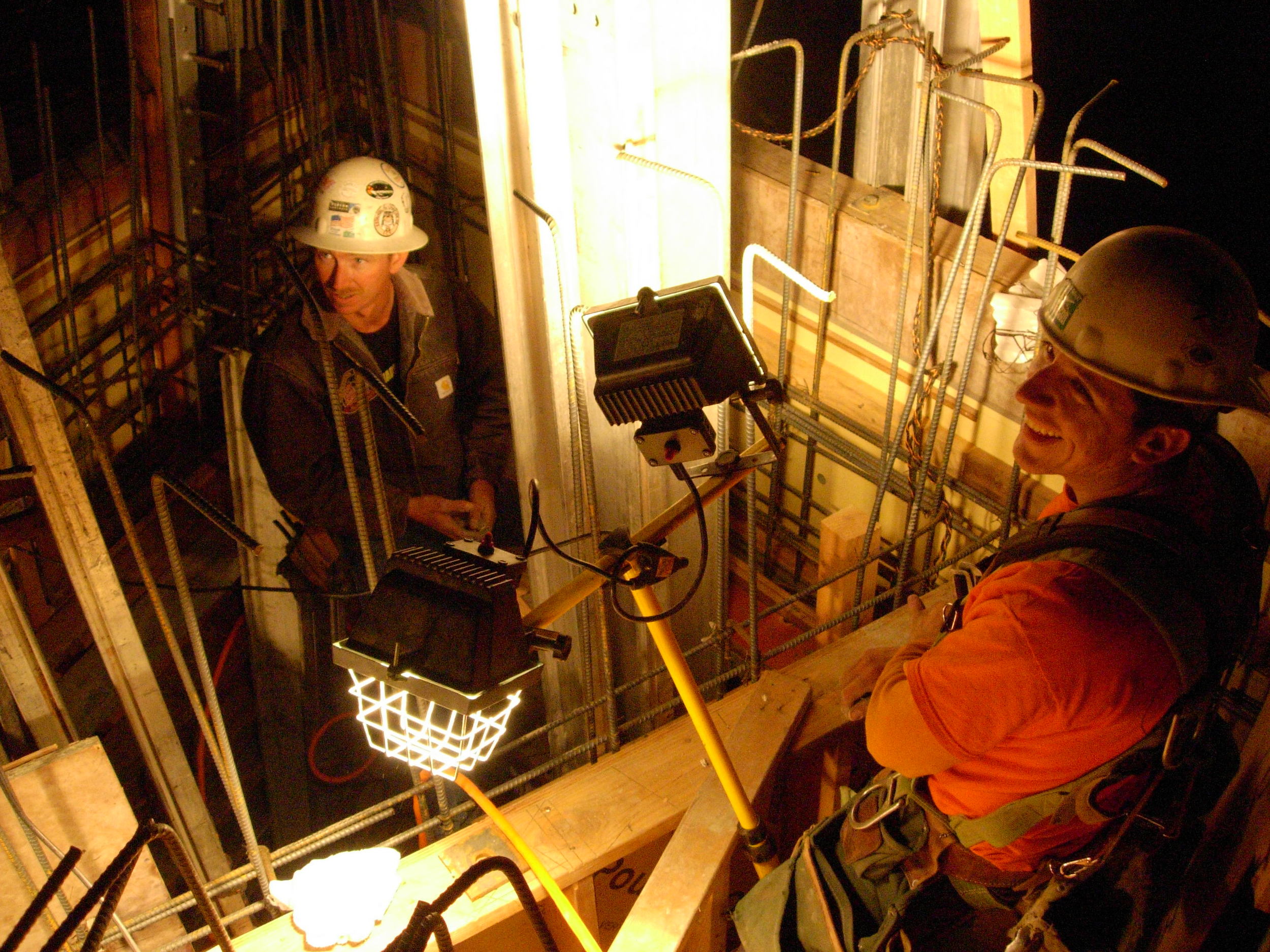
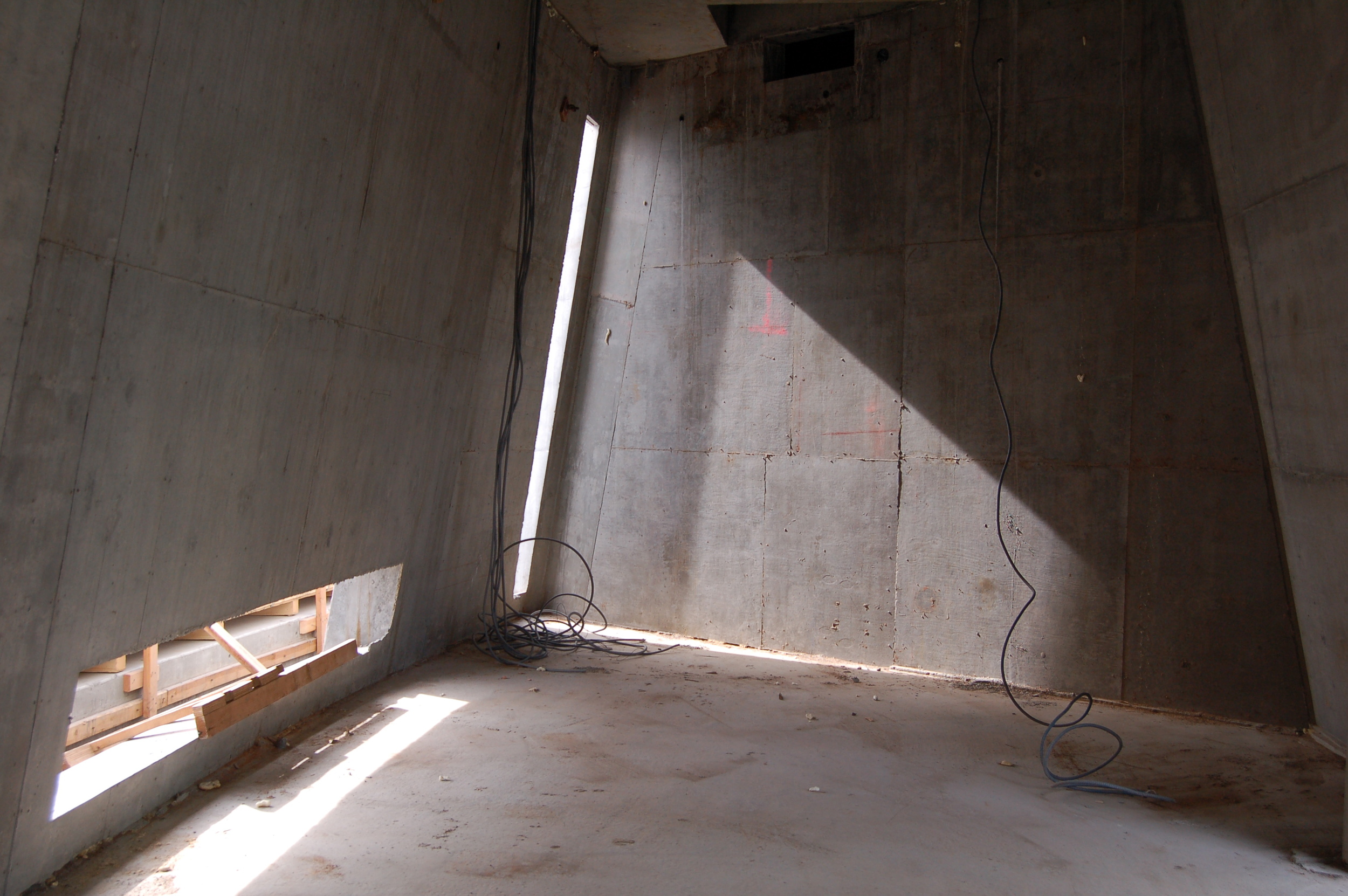
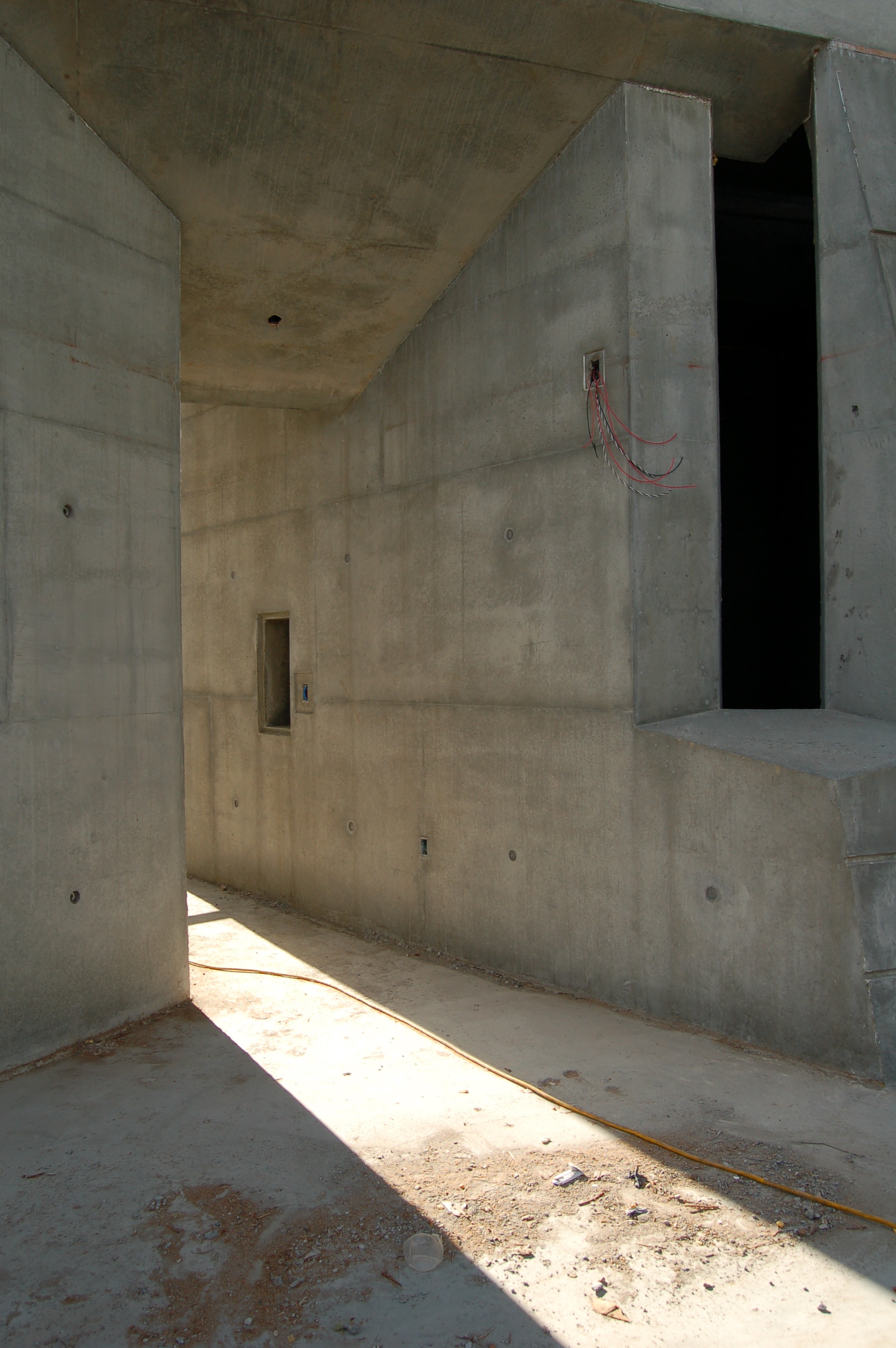
Interestingly, this was to become a common theme through the design-to-construction process for many elements of the Cathedral. The complexity of the geometry and patterns we created often made traditional means of documentation both cumbersome and inadequate, and yet there was no established protocol among the different parties for exchanging information of this sort - no agreement that 3D models or laser cutting files, etc. were adequate as source material. We spent a great deal of time in meetings navigating towards consensus of what forms documentation would take. In most cases, I was lucky to have direct contact with fabrication teams so that we were able to establish a line of communication between designers and fabricators that was crucial to getting everything built on time. However, we were also compelled to generate a number of document sets which included ridiculously dense data reports that were provided as a back up of sorts to the digital files, but I would surmise went unused.
Having worked on all of the drawings, it was logical for me to come out with each stage to begin reviewing the carpentry once the formwork started to go up on site. It was during these sessions that I began to establish a relationship with the construction crew. In one of my first outings, I caught a large error that the formwork carpenters had missed – at the bottom edge on a number of a pieces of blockout formwork that would eventually become a series of floor level windows carved out of the concrete, they had left a huge gap – easily exceeding ½’-3/4” in some places. It was an understandable oversight – the gap was the result of having to attach a large blockout form onto a curved/sloped wall with a joint that you couldn’t see or find unless you literally got down on your hands and knees and ran your finger along the gap. Leaving it as is would allow concrete to leak through and ruin the edge of a feature opening and would require post-cure cutting and patching. Fixing it would require that the crew rip out all the work and start again. To their credit, the carpenters remained civil through the exchange, though they were clearly very angry and frustrated. Later down the road, however, I was so pleased when the head carpenter singled me out on site during a subsequent formwork review and requested that I look at all of the joints for the blockouts that had been revised. They were perfect! The carpenters had done a beautiful job of reworking the forms so that they met the curvature of the walls seamlessly. So much so that they had also revised their method of applying joint filler because the gap was now so small they needed a smaller tip and more refined method of application to adjust to the narrowed gap. I was thoroughly impressed with the obvious pride of work that had replaced the frustration of the previous day. From that point on, the only issues we had with formwork were minor.
One concrete pour was scheduled for a weekend and I took advantage of my access to the site to spend the day with the crew to observe the process. I was able to talk to the foreman sent with the concrete subcontractor and was lucky to get a great explanation of how self-consolidating concrete was reviewed in the field via a slump test, which I caught on video.